More information about FK1-2 and FK1-6
Specifications:
- Long tube filling.
- Bottles, diameter: 60 – 90mm.
- Bottles, height: 180 – 300mm.
- Adjusting the machine for different bottle sizes is made by manually adjusting guides, filling- and capping heads. Time needed is approximately 2 hours.
- The shape of the bottles is not important as long as they have a lower cylindrical part.
- Caps: 26 mm.
- Capacity: 2- heads up to 600 bottles per hour depending on product.
- Capacity: 6- heads up to 1800 bottles per hour depending on product.
- Feed out buffer: Approx. 60 bottles depending on size.
- Most compact equipment on the market.
NOTE!: Machine with 2-heads can later be expanded to 6-heads and should be seen as a machine to grow in!
Oxygen
- The filling tubes have integrated tubes for CO2 that start to blow CO2 as soon as the tubes pass the bottle neck. How long it will blow CO2 through the bottle, before the pressure is built up, can be adjusted on the HMI.
- Possibility to add CO2 to top of bottle after filling.

Foam
- Counter pressure adjustable between 0 and 2,5 bars.
- Filling speed adjustable from 0-100% in three different steps, start-, main-, and end flow.
- Decompression adjustable in multiple steps.
Adjustments can be made on the HMI while running.
Gives a unique possibility to optimize filling depending on type of beer, temperature and CO2 level.
- Beer with up to 6,8 g/l CO2, with a temperature of 4 degrees Celsius after bottling, has been bottled in the machine. It is very slow but, depending on beer type, it is possible.
Washing
- The machine has an automatic washing program easily controlled by the HMI.
HMI and operator instructions
- The HMI is a 10” touch screen (Allen -Bradley) with symbols, text and explanations for all functions. It also shows alarms and functions visually, with explanations and suggested actions of what to check and how to solve possible problems.
- Most instructions can be found in the HMI. If not – in the documentation.
- Examples of screens:

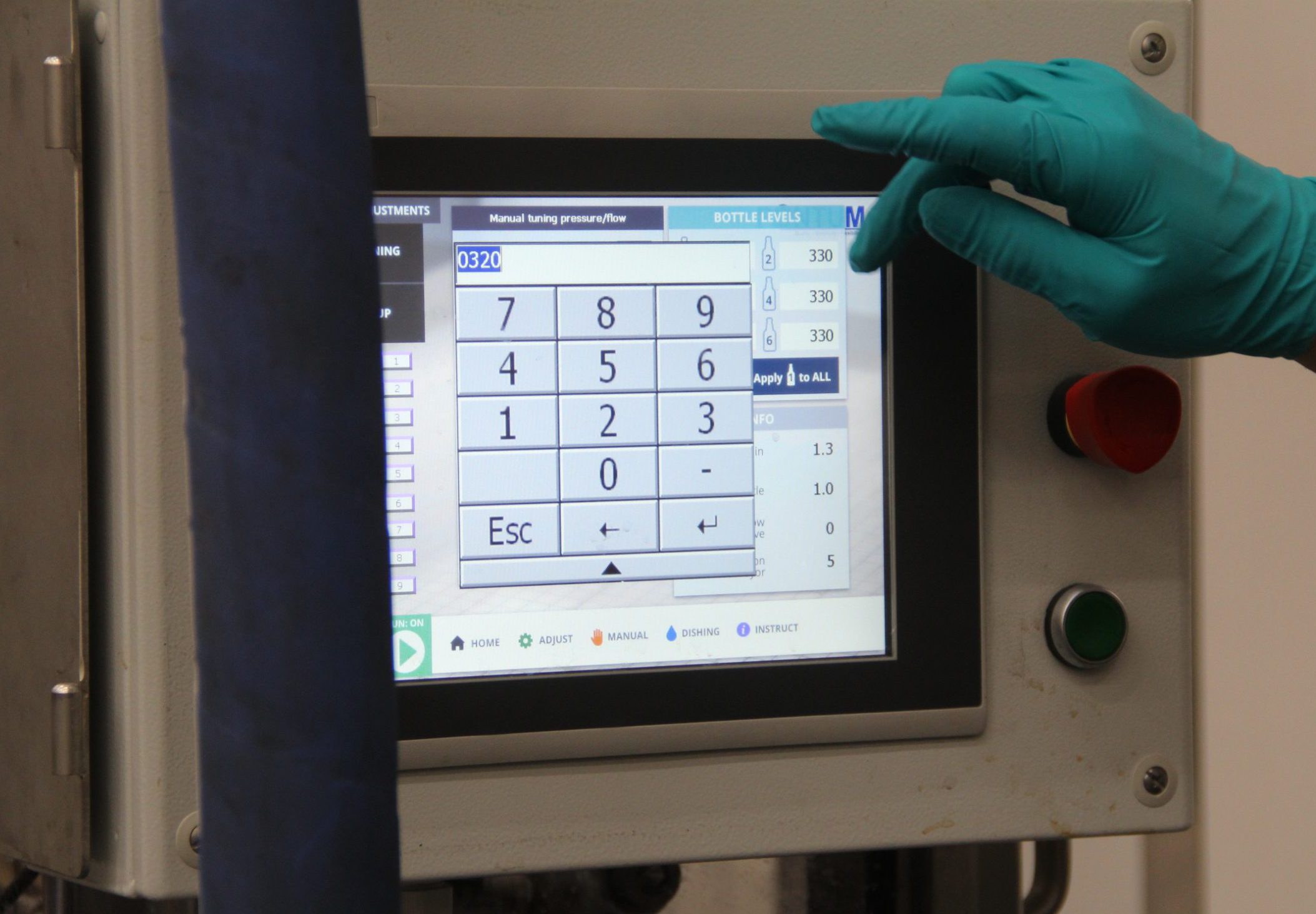
Automatic cap sorting:
A container on the top of the machine is filled with caps. The caps are automatically sorted and fed to the capping head. The container holds enough caps for ca 30min of production.
Feed out table prepared for box packaging:
Feed out table for the finished bottles. Room for ca 60 bottles. From this table the bottles are packed into the boxes. It is prepared for future automation of box packaging. Feed out table can be folded to take up less space when not in use.
Components and material:
Manufactured parts: Stainless of minimum EN 1.4301
Surface treatment: Ground/brushed, minimum K180
Pneumatic components: SMC ISO/VDMA
Linear guides: Raydent treated and/or stainless, standard measures. Made in Germany and Korea.
PLC and el. components: Rockwell Automation (Allen-Bradley)
Hoses and valves: FDA approved
Other components: Industrial standard
Supply specifications
Compressed air: ca 500l/min, 6 bar +-0,3 bar
El: 230/240V 10A
Power consumption: < 2kW
CO2: Pressure min: 2,5 bar. Thread 1/8” or ¼”.
Inflow of beer: Via hose from pressure tank or pump ca 1-2 bar. Thread for hose Male DIN25.
We use components from leading suppliers with worldwide sales and service
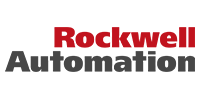
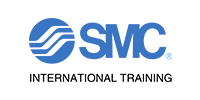
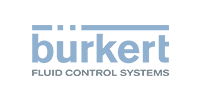
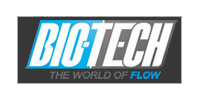
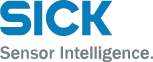
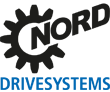
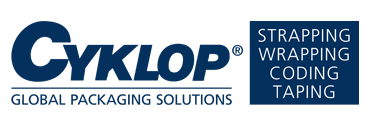
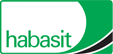